POWERGRIPS
As a fourth year engineering student at UVic, you’re required to take part in the Capstone projects. These are opportunities to flex your knowledge and showcase any skills you’ve developed.
For this reason, I had come up with a design project over the prior year in preparation. The POWERGRIPS gauntlet (acronym necessary of course), was developed as a control mechanism for inputting commands into a bionic arm. As a concept, the gauntlet could be worn on an amputee’s able arm, while not impacting dexterity and supply controls to an actuated prosthetic device.

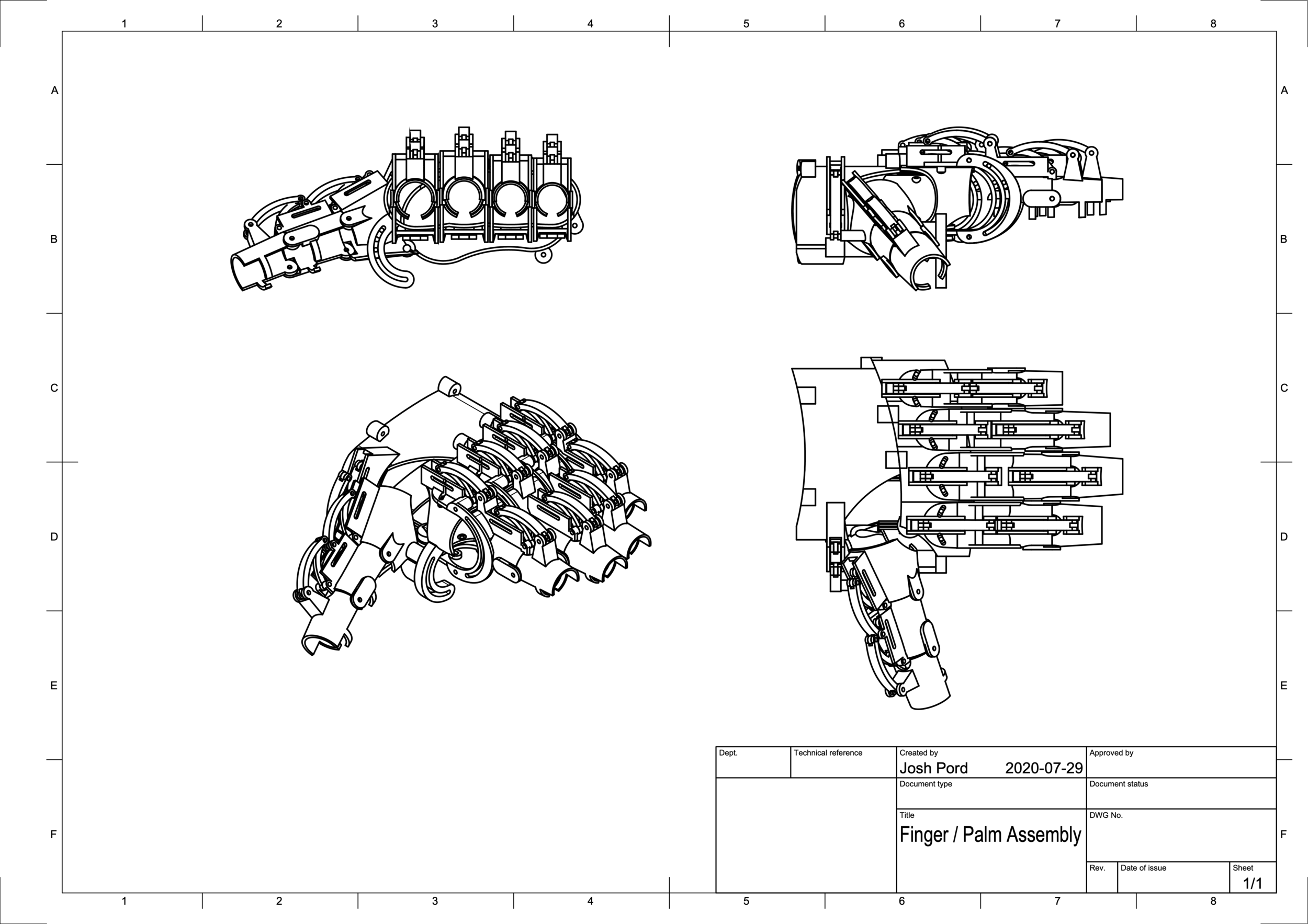
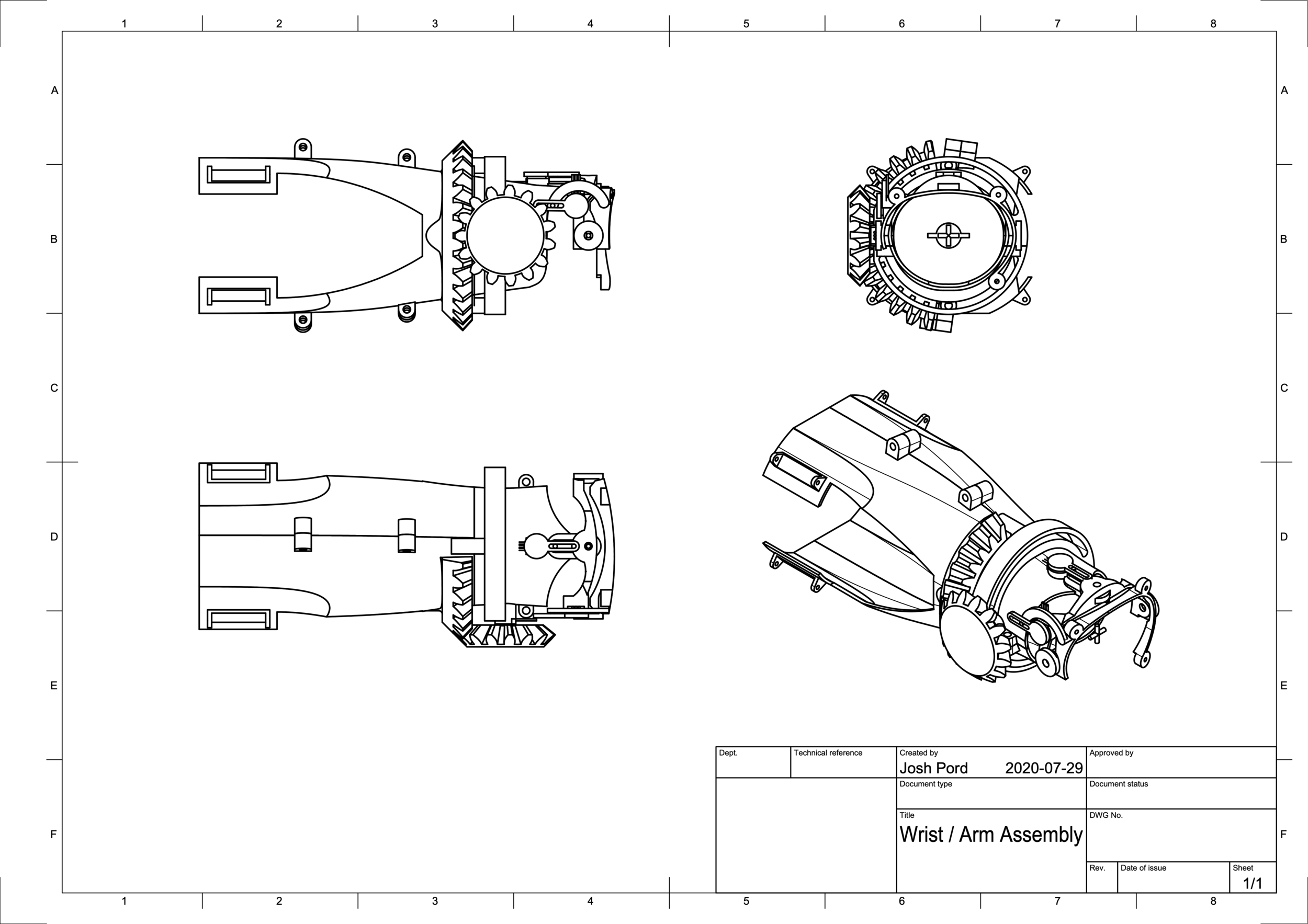
The actual project
To develop a physical prototype for testing, the team had 3 months and 175$ to complete the job. Once the team was formed, the project got off the ground. Luckily everyone was onboard with the concept and were willing to invest the effort.
For the initial 3D prints of the prototype, resin SLA was used. Mostly this was because it was initially available, but also since the dimensions of certain fittings were only a couple millimetres. This first run of prototype parts gave good feedback on immediate modifications that were needed, but most of them failed. For the following prototypes and any further prints, PLA filament printers were used.
With the change in materials, the number of iterations could be increased. In total, we were able to make 5 generations of the design. This resulted in a prototype that could test almost all of the project goals the team had set out, without needing to compromise. The desired range of motion in all four fingers and the wrist could be measured. Wearing the gauntlet also didn’t impact the dexterity of the user, allowing them to continue any actions they’d wanted to without restriction.
Once the prototype was actually created, the potentiometer were wired and secured in place. 18 total degrees of freedom are measured, output through the microcontroller and interpreted by the computer. Two software programs were written, one to catalogue the motion through a learning algorithm and the other for display. Since we don’t have access to any bionic arms, the laptop is meant as a stand-in for the application and acted as the finish line.
It was really unbelievable when we all saw the 3D model move to the control input. Even though our resources were limited, the team’s hard work, communication and planning made it come together. Just in time.